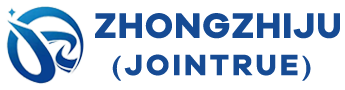
当前位置:首页>>NEWS>>Industry news
Industry news
In aluminum ingot forging, even after a longer period of time, for example, white spots are often several hours or dozens of hours after the forging is cooled to room temperature. After cooling, no white spots were found at 122448h, and no white spots were found at 72h. In addition, after the occurrence of white spots, new white spots will be generated and expanded from time to time during the subsequent cooling and storage. Therefore, the inspection of white spots should be carried out at intervals after cooling.
White spots can not be formed, but if the hydrogen content is high, there are many theories about the formation of white spots. But the white spot which is more convincing and can be proved by practice is the result of the joint action of hydrogen and structural stress in steel. The structural stress here mainly refers to the internal stress formed when austenite transforms into martensite and pearlite. There is not a certain amount of hydrogen and more significant tissue stress. However, the stress of the structure is not large, and generally there will be no white spots. For example, for single-phase austenitic and ferritic steels, there are less white spots because there is no transformation stress.
The plasticity of the steel is reduced. When the hydrogen content reaches a certain value, how does hydrogen and tissue stress promote the formation of white spots? At present, the understanding of these problems is as follows: 1. The plasticity drops sharply, resulting in hydrogen embrittlement. Especially when the stress exists in the steel for a long time, hydrogen can diffuse to the stress concentration region (the hydrogen atoms dissolved in the gap tend to concentrate in the lattice receiving tensile stress) and make its plasticity almost equal to zero. Brittle fracture occurs when the stress is large enough. For example, when 25cr2ni2mo steel contains 14.5cm3100g hydrogen, it is normalized at 900 ℃ and tempered at 600 ℃, the elongation decreases to 0.6% and the reduction of area decreases to 0.20. When 25cr2ni2mo steel contains 7.84cm3100g hydrogen, the elongation and reduction of area in quenched state decrease to 0.2% and the reduction of area decreases to 0. When 25cr2ni2mo steel contains 170cm3100g hydrogen, the elongation in annealed state decreases to 0.2% and the reduction of area decreases to 0, The elongation and reduction of area in quenched state are both reduced to 02. Hydrogen absorbed in molten steel during steelmaking is precipitated due to the decrease of solubility during ingot solidification. There is no time to escape from the surface of ingot and exist in the internal gap of ingot. Hydrogen dissolves in the steel again when heated before pressure processing. During the cooling process after pressure processing, due to the decomposition of austenite and the decrease of temperature, the solubility of hydrogen in the steel decreases, and hydrogen atoms precipitate from the solid solution to some micro voids in the billet. In addition, the reaction of hydrogen with carbon in steel to form methane (CH4) also results in high molecular pressure. This is confirmed by the decarburization phenomenon on the surface of some white spots; 3. Under certain conditions, the structural stress caused by phase transformation can reach a considerable value (the more serious the dendrite segregation, the faster the cooling rate and the better the hardenability of the steel, the greater the structural stress). Therefore, the hydrogen embrittlement of the steel loses its plasticity. Under the combined action of the structural stress and the internal stress caused by hydrogen precipitation, the brittle fracture of the steel occurs, This creates a white spot. The additional stress caused by non-uniform deformation and the thermal stress during cooling also have some influence on the formation of white spots. Because there are many large voids in cast steel, hydrogen precipitation will not cause great internal stress, so it is not sensitive to white spots. Ferrite and austenite steels generally do not appear white spots because there is no phase transformation and no structural stress during cooling. Although ledeburite steels have large structural stress during cooling, it may be due to the formation of stable hydrides by hydrogen in these steels and the complex carbides hindering the precipitation of hydrogen, and there is no white spot.